Troubleshooting Common Emulsion Mistakes and How to Fix Them
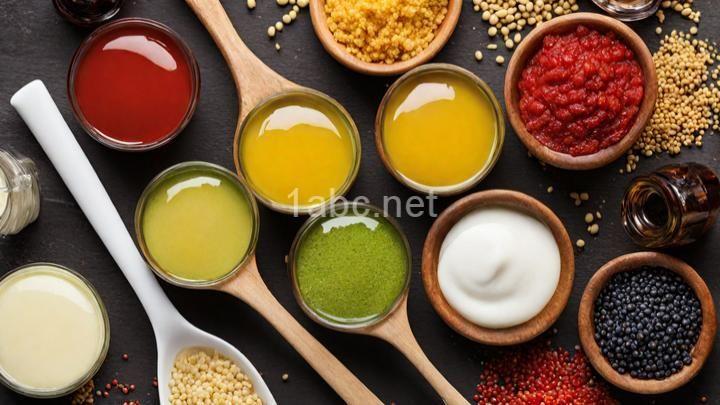
Introduction:
Screen printing is a versatile and popular method for creating vibrant and durable designs on various surfaces. At the heart of this printing technique lies emulsion, a crucial component that acts as a stencil for transferring the design onto the printing surface. However, even the most experienced screen printers can encounter issues with emulsion, leading to flawed prints and frustration. In this blog post, we will explore some common emulsion mistakes and provide practical solutions to help you troubleshoot and overcome these challenges.
I. Understanding Emulsion Basics
A. What is emulsion?
Emulsion is a light-sensitive substance that consists of two components: a photosensitive polymer and a sensitizer. It is typically in liquid form and is applied to a mesh screen to create a stencil for printing. When exposed to light, the emulsion hardens, creating a barrier that allows the ink to pass through only where the design is intended.
B. How does emulsion work in screen printing?
In screen printing, emulsion is coated onto a clean and dry screen using a scoop coater or a similar tool. The screen is then dried to ensure that the emulsion is evenly distributed and ready for exposure. After the desired design is applied to the screen, it is exposed to light, which causes the emulsion to harden in the exposed areas. The unexposed emulsion can then be washed away, leaving behind a stencil ready for printing.
C. Different types of emulsion available
There are several types of emulsion available, each with its own unique properties and suitability for different printing needs. Some common types include dual-cure emulsion, diazo emulsion, and photopolymer emulsion. It's important to choose the right emulsion for your specific printing requirements, taking into account factors such as ink compatibility, durability, and resolution.
II. Common Emulsion Mistakes and Solutions
A. Mistake 1: Improper Mixing or Dilution
One of the most common mistakes in working with emulsion is improper mixing or dilution. This can lead to issues such as inconsistent coating, poor image quality, and difficulty in reclaiming screens. To avoid these problems, it's crucial to follow the manufacturer's instructions carefully.
To mix emulsion correctly, start by pouring the emulsion into a clean container. Then, add the recommended amount of water or diazo sensitizer, depending on the emulsion type. Use a stirring stick or a mixer to thoroughly mix the emulsion until it reaches a smooth and homogeneous consistency. Remember to wear gloves and follow safety precautions when handling emulsion and sensitizer.
B. Mistake 2: Uneven Coating
Uneven coating can result in areas of the design being too thick or too thin, leading to print inconsistencies and potential ink leakage. To achieve a smooth and even coat of emulsion, there are several factors to consider.
First, ensure that the screen is clean and free from any dust or debris. Any particles on the screen can disrupt the even spread of the emulsion. Use a screen degreaser or a mild detergent to clean the screen thoroughly before coating.
Next, choose the appropriate mesh count for your design. Finer mesh counts are suitable for intricate details, while coarser mesh counts work well for bold and solid designs. The mesh count affects the thickness of the emulsion layer, so choose wisely.
To apply the emulsion, use a scoop coater or a similar tool. Start at the bottom of the screen and slowly drag the coater upwards, applying even pressure. Repeat this process a few times to ensure an even and consistent coat across the entire screen. If necessary, use a squeegee or a coating trough to distribute the emulsion evenly.
C. Mistake 3: Overexposure or Underexposure
Overexposure or underexposure can result in image distortion, decreased clarity, and difficulty in reclaiming screens. Proper exposure is crucial to achieve sharp and accurate prints.
To determine the correct exposure time, perform a test with a step wedge or a test print. This involves exposing the screen with different exposure times and then evaluating the results. Look for well-defined edges, crisp details, and solid areas of the design. Adjust the exposure time accordingly until the desired results are achieved.
Factors such as the type of emulsion, mesh count, artwork complexity, and light source intensity can affect the exposure time. Regularly monitor and calibrate your exposure unit to ensure consistent and accurate results.
D. Mistake 4: Inadequate Drying Time
Insufficient drying time before exposure can lead to premature emulsion hardening and difficulty in washing out the unexposed areas. It's important to allow the coated screens to dry completely before exposing them to light.
To ensure proper drying, place the screens in a clean and dust-free area with good air circulation. You can use a fan or a dehumidifier to speed up the drying process, but avoid direct heat sources as they can cause the emulsion to dry unevenly or warp the screen.
Check the screens for dryness by touching the emulsion with a gloved finger. If the emulsion feels tacky or leaves a residue on your finger, it needs more drying time. Patience is key, as rushing this step can result in costly mistakes.
E. Mistake 5: Poor Reclaiming Practices
Improper cleaning and reclaiming of screens can lead to ghost images, emulsion residue, and decreased stencil lifespan. To maintain the longevity of your screens and ensure clean prints, effective reclaiming practices are essential.
Start by removing any excess ink from the screen using a plastic scraper or a screen washout booth. Then, apply a screen degreaser or a stencil remover to dissolve the emulsion. Use a soft brush or a pressure washer to scrub the screen gently, paying attention to the corners and edges.
Rinse the screen thoroughly with water to remove all traces of emulsion and cleaning agents. Inspect the screen for any remaining residue or ghost images, and repeat the cleaning process if necessary. Finally, dry the screen completely before reapplying emulsion for your next print run.
III. Preventing Future Emulsion Mishaps
A. Proper Storage and Handling Tips
To prolong the shelf life of your emulsion and maintain its quality, proper storage and handling are crucial. Emulsion should be stored in a cool and dark place, away from direct sunlight and extreme temperatures. Close the container tightly after each use to prevent air exposure, which can lead to premature degradation.
When handling emulsion, wear gloves and protective clothing to avoid direct contact with the skin. Follow safety guidelines provided by the manufacturer to ensure personal safety and minimize health risks. If the emulsion expires or shows signs of degradation, it's best to dispose of it properly and replace it with fresh emulsion.
B. Regular Maintenance Routine
Regular maintenance is essential to prevent issues and ensure a smooth printing process. Develop a routine for cleaning and inspecting your screens and equipment.
After each print run, clean the screens thoroughly to remove any ink residue or buildup. Inspect the screens for any damage or wear and tear, such as frayed edges or holes in the mesh. Address any issues promptly to avoid further complications.
Clean and maintain your exposure unit, drying rack, and other equipment according to the manufacturer's instructions. Regularly check and replace any worn-out or damaged parts to ensure optimal performance.
Conclusion:
Troubleshooting common emulsion mistakes in screen printing requires attention to detail, patience, and a willingness to learn and adapt. By understanding the basics of emulsion, identifying common mistakes, and implementing the suggested solutions, you can overcome challenges and improve the quality of your prints.
Remember to follow the manufacturer's instructions for emulsion mixing, coating, exposure, and reclaiming. Practice proper storage and handling techniques to extend the shelf life of your emulsion. Additionally, prioritize regular maintenance to prevent issues and ensure consistent results.
We hope this guide has provided you with valuable insights and practical tips for troubleshooting emulsion mistakes in screen printing. Don't be discouraged by setbacks; they are opportunities for growth and improvement. With practice and persistence, you'll become more confident in your screen printing skills and achieve the desired results in your prints.
If you have further questions or need additional assistance, feel free to reach out to us. Happy printing!
FREQUENTLY ASKED QUESTIONS
How can I prevent emulsion mistakes?
To prevent emulsion mistakes, there are several steps you can take to ensure a smooth and successful process. Here are some tips to help you avoid common pitfalls:
-
Use compatible ingredients: Emulsions require a combination of oil and water-based ingredients. Make sure that the ingredients you use are compatible and can form a stable emulsion. For example, using an oil and water that do not mix well can result in separation or a broken emulsion.
-
Temperature control: Emulsions are often formed by combining ingredients at specific temperatures. Pay attention to the recommended temperature range for each ingredient and follow the instructions closely. Extreme temperatures can affect the stability of the emulsion and lead to separation.
-
Slow and steady mixing: When combining the oil and water phases, it's important to mix slowly and steadily to allow the emulsion to form properly. Avoid vigorous mixing or using high-speed blending, as this can introduce air bubbles and disrupt the emulsion.
-
Use emulsifiers: Emulsifiers play a crucial role in stabilizing emulsions by reducing the surface tension between oil and water. Adding emulsifiers, such as lecithin or beeswax, can greatly improve the stability of your emulsion and prevent separation.
-
pH balance: Consider the pH levels of your ingredients, as it can impact the stability of your emulsion. Some ingredients may require adjustments to reach an optimal pH range for emulsion formation. A pH meter or pH test strips can help you monitor and adjust the pH as needed.
-
Storage conditions: After preparing your emulsion, store it in suitable containers and under proper conditions. Keep the emulsion away from excessive heat, cold, and direct sunlight, as these factors can destabilize the emulsion over time.
By following these guidelines, you can minimize the chances of emulsion mistakes and create successful emulsions for your desired applications. Remember to experiment and adjust your process as needed to achieve the desired results.
How do I fix a curdled emulsion?
To fix a curdled emulsion, there are a few steps you can take. First, remove the curdled mixture from the heat source immediately. Next, try adding a small amount of cold water or another liquid that is part of the recipe, such as vinegar or lemon juice. Slowly whisk or blend the mixture together until it starts to come together again. If the emulsion is still not fully smooth, you can try using an immersion blender to further blend the ingredients. Another option is to strain the mixture through a fine-mesh sieve to remove any remaining lumps or curdled bits. Lastly, if all else fails, you may need to start over and make a fresh batch of the emulsion. Remember, emulsions can be tricky, so it's always a good idea to follow the recipe carefully and pay attention to temperature and ingredient ratios.
Why does emulsion separation occur?
Emulsion separation occurs due to the immiscibility of certain substances. An emulsion is a mixture of two or more liquids that are normally unmixable, such as oil and water. When these liquids are combined, they form tiny droplets that are dispersed throughout the mixture.However, over time, these droplets can start to coalesce and separate, leading to the formation of distinct layers. This separation is driven by various factors, including differences in density, viscosity, and surface tension between the liquids.
Density plays a significant role in emulsion separation. If one liquid has a higher density than the other, it tends to sink to the bottom, causing the emulsion to separate into layers. Viscosity, or the resistance to flow, also affects emulsion stability. Liquids with high viscosity are more likely to resist mixing and separate over time.
Surface tension, which is the force that holds the surface of a liquid together, can also contribute to emulsion separation. If the surface tensions of the two liquids in the emulsion are significantly different, the droplets may start to merge and eventually separate.
Other factors that can influence emulsion stability include temperature, agitation, and the presence of emulsifiers or stabilizers. Temperature changes can cause the liquids to expand or contract, altering their behavior and potentially leading to separation. Agitation, such as stirring or shaking, can disrupt the emulsion and promote separation. Emulsifiers and stabilizers, on the other hand, help to prevent separation by reducing the interfacial tension between the liquids and enhancing their compatibility.
Understanding the reasons behind emulsion separation can be helpful in preventing or managing it. By considering the properties of the liquids involved and utilizing appropriate techniques or additives, such as emulsifiers or stabilizers, it is possible to maintain the stability of emulsions and prevent unwanted separation.
How can I fix emulsion separation?
To fix emulsion separation, you can try a few simple steps:
-
Gently shake the container: Emulsion separation occurs when the oil and water in a mixture start to separate. Give the container a gentle shake to try and recombine the two components.
-
Heat and stir: If shaking doesn't work, try heating the mixture slightly and stirring it vigorously. The heat helps to break down any clumps and the stirring helps to mix the oil and water back together.
-
Use an emulsifier: If the separation persists, you can try adding an emulsifier to the mixture. Emulsifiers help to stabilize the mixture and prevent separation. Common emulsifiers include egg yolks, mustard, or lecithin.
-
Store properly: Sometimes, emulsion separation occurs due to improper storage. Make sure to store the mixture in a cool, dry place and avoid extreme temperature fluctuations.
Remember, every emulsion is different, so the effectiveness of these steps may vary. It's important to experiment and find the best solution for your specific situation.