How to Prepare Your Subfloor for a Successful Floor Installation
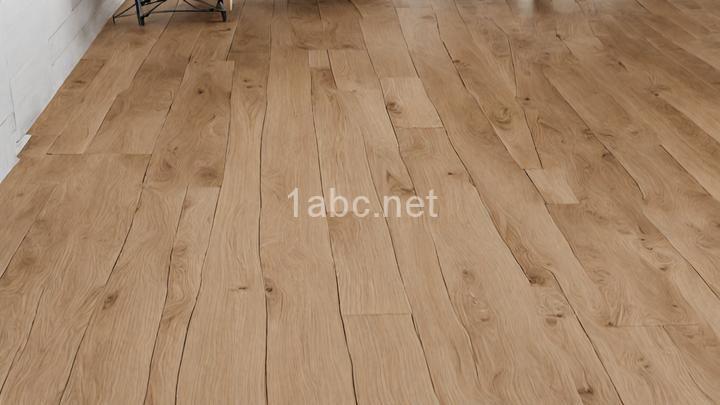
Introduction:
Welcome readers to this blog post, where we will discuss the importance of preparing your subfloor before installing new flooring. Whether you're planning to lay down hardwood, carpet, vinyl, or any other type of flooring, proper subfloor preparation is key to achieving a successful and long-lasting installation. But don't worry, with the right information and guidance, you'll be well-equipped to tackle this crucial step and ensure a beautiful and durable floor in your home.
I. Assessing the Subfloor Condition:
Before diving into any project, it's essential to assess the condition of your subfloor. This step will help you identify any underlying issues that may affect your new flooring's stability and longevity. Start by inspecting the subfloor for unevenness, moisture problems, or damage. Unevenness can cause your new floor to become uneven or develop gaps, while moisture problems can lead to mold, mildew, or warping. Damaged subfloors, such as rotting wood or cracks, may require additional repairs.
To identify unevenness, grab a level and place it on various areas of the subfloor. If you notice significant deviations from a level surface, consider using a self-leveling compound to even it out. For moisture problems, check for signs of water damage, such as discoloration, musty odors, or soft spots. If you suspect moisture issues, perform moisture testing using a hygrometer or conduct a calcium chloride test to determine the moisture levels accurately.
In the case of damaged subfloors, assess the extent of the damage and determine whether it can be repaired or if professional help is needed. For minor damage, you may be able to replace the damaged sections yourself. However, when dealing with extensive damage or working with power tools, it's always advisable to consult a professional to ensure safety and structural integrity.
II. Removing Old Flooring:
Now that you've assessed the subfloor and addressed any underlying issues, it's time to remove the old flooring. Different types of flooring require different removal methods, so let's explore a few common ones.
-
Carpet: Start by cutting the carpet into manageable sections and roll them up for easy removal. Use a pry bar or pliers to remove any attached padding or tack strips. Vacuum thoroughly to remove any remaining debris or dust.
-
Hardwood: For hardwood flooring, you'll need to use a pry bar or floor scraper to gently lift and remove the boards. Take care not to damage the subfloor during this process. If the hardwood is glued down, consider using a heat gun to soften the adhesive before lifting the boards.
-
Vinyl: Begin by cutting the vinyl into strips or sections using a utility knife. Pry up the vinyl using a pry bar or putty knife, being cautious not to gouge or damage the subfloor. Remove any remaining adhesive using adhesive remover or a heat gun.
Remember to wear protective gear, such as gloves and safety glasses, during the removal process. Additionally, ensure proper ventilation in the room to minimize dust and fumes.
III. Cleaning and Leveling:
Now that your old flooring is out of the way, it's time to clean and level the subfloor. Cleaning the subfloor is crucial to remove any debris, dust, or adhesive residue that could affect the new flooring's adhesion. Use a broom, vacuum, or mop to thoroughly clean the subfloor. If adhesive residue remains, consider using an adhesive remover or scraping it off using a putty knife.
Next, let's address any unevenness in the subfloor. If you've noticed significant deviations from a level surface, you have a few options to level it out. One popular method is using a self-leveling compound, which is a fluid material that spreads out and levels itself when poured onto the subfloor. Follow the manufacturer's instructions to mix and apply the compound, ensuring even coverage. Allow it to dry according to the recommended drying time before proceeding with the installation.
Alternatively, if the subfloor requires additional structural support, consider using a plywood underlayment. This involves installing a layer of plywood over the subfloor to create a level and sturdy surface for the new flooring. Measure and cut the plywood sheets to fit the room, leaving a small gap of around 1/8 inch between the sheets to allow for expansion. Secure the plywood to the subfloor using screws or nails, making sure to stagger the seams for added stability.
IV. Addressing Moisture Issues:
Moisture is one of the most significant threats to the integrity of any flooring installation. Excessive moisture can lead to warping, mold, and even structural damage. Therefore, it's crucial to address any moisture issues before proceeding with the installation.
If you suspect high moisture levels in your subfloor, you can perform moisture testing to confirm. One method is using a hygrometer, which measures the relative humidity in the air. Place the hygrometer in different areas of the room to obtain accurate readings. Another common method is the calcium chloride test, which involves placing a moisture-absorbing pad on the subfloor for a specified period. The pad is then analyzed to determine the moisture levels.
If moisture levels are high, consider applying a vapor barrier to prevent moisture from seeping into the new flooring. A vapor barrier is a moisture-resistant material, such as plastic sheeting, that is installed over the subfloor to create a barrier between it and the flooring. Additionally, using waterproofing products, such as sealants or primers, can provide an extra layer of protection against moisture.
V. Repairing Damaged Subfloors:
If your subfloor has any noticeable damage, it's essential to address it before proceeding with the installation. Damaged subfloors can compromise the stability and longevity of your new flooring. Let's explore some common types of subfloor damage and possible repair techniques.
-
Rotting Wood: If you notice rotting wood in your subfloor, you'll need to replace the damaged sections. Start by cutting out the damaged portions using a circular saw or reciprocating saw. Take measurements of the removed sections and cut replacement pieces accordingly. Secure the new pieces in place using screws or nails, ensuring a snug fit.
-
Cracks: Cracks in the subfloor can be problematic, especially if they are significant or extend beyond the surface. Small cracks can often be repaired using a wood filler or epoxy. Clean the crack thoroughly and apply the filler or epoxy according to the manufacturer's instructions. Allow it to dry completely before proceeding with the installation.
When dealing with subfloor repairs, it's essential to prioritize safety. Wear protective gear, such as gloves and eyewear, and take necessary precautions when working with power tools or handling potentially hazardous materials.
VI. Preparing Subfloors in Specific Scenarios:
In addition to the general guidelines we've discussed so far, there are some specific scenarios that require additional consideration when preparing the subfloor. Let's explore a few of them:
-
Concrete Subfloors: Concrete subfloors require specific preparation to ensure proper adhesion and prevent moisture issues. Start by cleaning the concrete thoroughly to remove any dirt, dust, or grease. Fill any cracks or holes using a concrete patching compound. Consider using a moisture barrier, such as an epoxy primer or moisture sealant, to prevent moisture from seeping into the new flooring.
-
Basement Installations: Basements often have unique challenges, including potential moisture issues and uneven surfaces. Before proceeding with a basement installation, perform a thorough moisture test to ensure the space is suitable for flooring. Address any moisture problems using appropriate methods, such as installing a vapor barrier or using waterproofing products. Additionally, use a self-leveling compound or plywood underlayment to level out any uneven subfloor areas.
-
Preparing for Tile: Tile installations require a stable and even subfloor to prevent cracks and damage to the tiles. Follow the general cleaning and leveling guidelines discussed earlier. Additionally, consider using a cementitious backer board or an uncoupling membrane, such as Schluter-DITRA, to provide an extra layer of stability and prevent tile movement.
Remember, each scenario may have its specific requirements, so it's essential to research and consult professionals if needed to ensure the best results.
Conclusion:
In conclusion, preparing your subfloor properly is a crucial step in achieving a successful floor installation. By assessing the subfloor condition, removing old flooring, cleaning and leveling, addressing moisture issues, and repairing any damage, you can create a stable and suitable surface for your new flooring. Remember to take your time, follow safety precautions, and seek professional assistance if needed. With proper preparation, you'll be well on your way to a beautiful and long-lasting floor in your home.
Closing Remarks:
Thank you for taking the time to read this blog post on preparing your subfloor for a successful floor installation. We hope you found the information helpful and informative. If you have any questions or need further assistance, please don't hesitate to leave a comment or reach out to us. We're here to help! Best of luck with your floor installation project, and we wish you many years of enjoyment with your new flooring. Farewell!
FREQUENTLY ASKED QUESTIONS
Why is it important to prepare the subfloor before installing a new floor?
Preparing the subfloor before installing a new floor is crucial for several reasons. First and foremost, it ensures a solid and stable foundation for your new flooring. By properly preparing the subfloor, you can prevent future issues such as creaking, sagging, or unevenness in the floor.Additionally, preparing the subfloor helps to extend the lifespan of your new flooring. If the subfloor is not properly leveled or cleaned, it can lead to premature wear and damage to your new floor, resulting in costly repairs or replacements down the line.
Another important reason to prepare the subfloor is to prevent moisture-related problems. Moisture can seep through an improperly prepared subfloor and damage the new flooring, causing it to warp, buckle, or develop mold and mildew. By taking the time to properly seal and protect the subfloor, you can minimize the risk of moisture-related issues and ensure the longevity of your new floor.
Lastly, preparing the subfloor allows for a smoother and more efficient installation process. By removing any existing flooring, cleaning the subfloor thoroughly, and addressing any imperfections or irregularities, you create a clean and level surface for the new flooring to be installed. This not only makes the installation process easier but also helps to achieve a professional and polished end result.
In conclusion, preparing the subfloor before installing a new floor is essential for ensuring a stable foundation, extending the lifespan of the flooring, preventing moisture-related problems, and facilitating a smooth installation process. By investing time and effort into preparing the subfloor, you can enjoy a beautiful and durable floor for years to come.
How do I know if my subfloor needs preparation?
To determine if your subfloor requires preparation, there are a few key factors to consider. First, you'll want to assess the condition of the existing subfloor. Check for any signs of damage such as cracks, unevenness, or rot. Additionally, inspect for any moisture issues, as excessive moisture can compromise the integrity of the subfloor and the flooring materials.Next, consider the type of flooring you plan to install. Different flooring materials have specific requirements for subfloor preparation. For example, hardwood flooring may require a flat and level subfloor, while vinyl or laminate flooring may tolerate slight irregularities.
It's also important to evaluate the existing subfloor's cleanliness. Remove any debris, dust, or old adhesive that could affect the installation of the new flooring.
If you're uncertain about the condition of your subfloor, it's advisable to consult with a professional. They can assess the subfloor and provide recommendations for any necessary preparation work. Taking the time to properly prepare your subfloor will help ensure a successful and long-lasting flooring installation.
What are some common subfloor preparation techniques?
When it comes to preparing the subfloor, there are several common techniques that can help ensure a smooth and durable flooring installation. Here are some of them:
-
Cleaning: The first step in subfloor preparation is to thoroughly clean the surface. Remove any dirt, dust, or debris using a broom, vacuum, or mop. This will create a clean and even base for the flooring.
-
Leveling: If the subfloor has any uneven areas or low spots, it may need to be leveled. This can be done by applying a self-leveling compound or using shims to raise the low areas. Leveling the subfloor will help prevent any gaps or irregularities in the final flooring.
-
Moisture Barrier: In areas where moisture is a concern, such as basements or bathrooms, it's important to install a moisture barrier. This can be a sheet of plastic or a specialized membrane that prevents moisture from seeping into the subfloor and causing damage to the flooring above.
-
Repairing Damaged Areas: If there are any damaged or rotten sections of the subfloor, they should be repaired or replaced before installing the new flooring. This could involve patching holes, replacing boards, or reinforcing weak areas to ensure a solid foundation for the flooring.
-
Removing Old Flooring: In some cases, the old flooring may need to be removed before preparing the subfloor. This is especially true if the old flooring is uneven, damaged, or incompatible with the new flooring material. Removing the old flooring will create a clean slate for the subfloor preparation.
-
Sanding and Smoothing: Depending on the type of flooring being installed, the subfloor may require sanding or smoothing. This is particularly important for hardwood or laminate flooring, as any imperfections in the subfloor can be visible through the new flooring. Sanding and smoothing will help create a level and smooth surface for the new flooring.
These are just a few of the common subfloor preparation techniques. The specific techniques required will depend on the condition of the subfloor, the type of flooring being installed, and any specific requirements or recommendations from the flooring manufacturer. It's always a good idea to consult with a professional or follow the manufacturer's guidelines for the best results.
How can I repair damaged areas on my subfloor?
To repair damaged areas on your subfloor, you'll need to follow a few steps:
-
Assess the damage: Take a close look at the damaged area and determine the extent of the problem. Is it a small hole, a crack, or a larger section that needs repair?
-
Remove any debris: Clear away any loose materials, such as splintered wood or chunks of subfloor, from the damaged area. This will help ensure a clean and smooth repair.
-
Cut out the damaged section: Using a circular saw or reciprocating saw, carefully cut out the damaged portion of the subfloor. Make sure to follow the lines of the existing subfloor to maintain a uniform shape.
-
Replace with new subfloor: Cut a new piece of subfloor to fit the opening you created. It's important to use the same thickness and type of subfloor material as the existing floor. Secure the new piece in place by screwing it into the floor joists.
-
Reinforce the repair: To strengthen the repair, you can install additional support by adding blocking or bridging between the floor joists around the repaired area. This will help prevent future damage or sagging.
-
Fill and level: Fill any gaps or seams with a wood filler or leveling compound. Smooth it out with a putty knife and let it dry according to the manufacturer's instructions.
-
Sand and finish: Once the repair is dry, sand the area to smooth out any rough edges or imperfections. Then, apply the appropriate finish, such as paint or stain, to match the surrounding floor.
Remember, if the damage to your subfloor is extensive or beyond your DIY skills, it's always a good idea to consult a professional contractor for assistance. They can help assess the situation and provide the best solution for your specific needs.